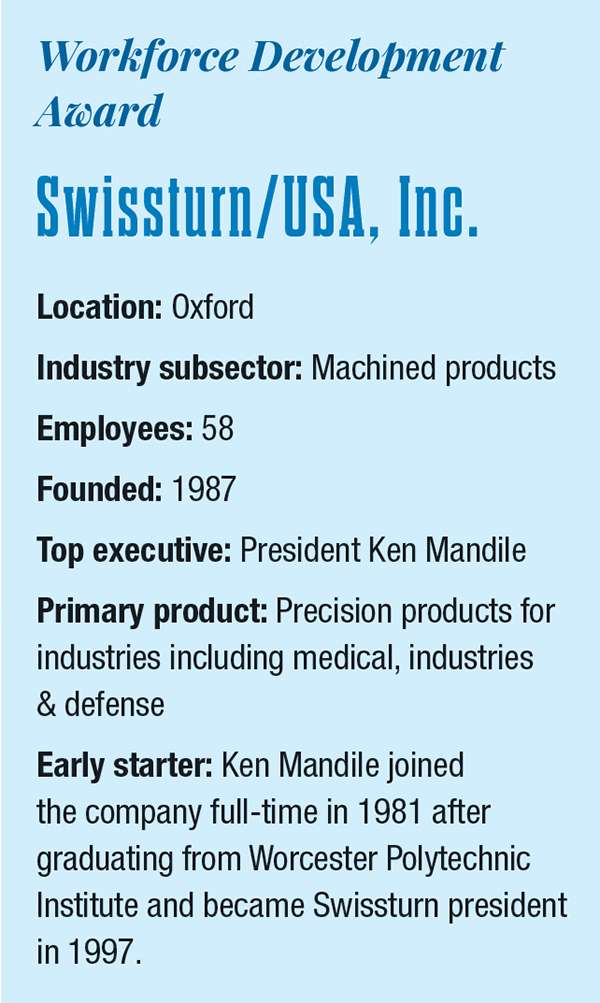
Please do not leave this page until complete. This can take a few moments.
Ken Mandile started working at the machine shop Swissturn/USA when he was just 10, learning from his father, who owned and ran the company at the time.
Decades later, owning and running the Oxford company himself, Mandile, now 61, saw few likely options for the company continuing on past his time leading it. So five years ago, he sold it – to Swissturn’s own employees.
The manufacturer became what’s known as an ESOP – an employee stock ownership plan giving Swissturn’s employees a 49% stake in the company. In the coming years, Mandile plans to make it 100%.
“We wanted to develop an ownership culture. This is my legacy. I’ve been doing this since I was 10 years old. I wanted to make sure it continued on,” Mandile said, recalling going to his employees with the idea. “I said, ‘I’d like you to meet the new owners. Look to the left and right of you.’”
Mandile is a strong advocate for ESOPs, learning about how they tend to lead to higher employee retention rates, high profits and lower turnover. They can also provide a significant retirement asset for workers and help reduce income inequality, he said.
With manufacturers often struggling to attract young workers and with an older workforce of 68 people, Swissturn has placed a priority on workforce development.
That begins with safety and regulatory training when an employee begins working there and continues with annual or biennial training with existing employees to keep them refreshed.
The company has worked with Auburn-based Massachusetts Manufacturing Extension Partnership, or MassMEP, which has helped Swissturn improve its organizational chart, job descriptions and other human resources aspects. In other cases, it has worked with other machine shops on collaborative projects to use job training grants, or hired through the Worcester-based Manufacturing Advancement Center Workforce Innovation Collaborative, known as MACWIC.
Mandile has heard the question: What if you spend so much time and effort training employees only for them to leave? He counters: What if you don’t train your employees and they don’t leave?
“We’ve always placed workforce development as a high priority for us,” he said.
Swissturn makes screws and other small machine parts, often stainless steel or brass, for medical, laser and electronic connector firms. But Swissturn workers are less focused on who they’re making the products for than simply building them – sometimes by the millions – by the exact specifications.
“A lot of times we don’t know what the product is,” Mandile said.
Stay connected! Every business day, WBJ Daily Report will be delivered to your inbox by noon. It provides a daily update of the area’s most important business news.
Sign upWorcester Business Journal provides the top coverage of news, trends, data, politics and personalities of the Central Mass business community. Get the news and information you need from the award-winning writers at WBJ. Don’t miss out - subscribe today.
SubscribeWorcester Business Journal presents a special commemorative edition celebrating the 300th anniversary of the city of Worcester. This landmark publication covers the city and region’s rich history of growth and innovation.
See Digital EditionStay connected! Every business day, WBJ Daily Report will be delivered to your inbox by noon. It provides a daily update of the area’s most important business news.
Worcester Business Journal provides the top coverage of news, trends, data, politics and personalities of the Central Mass business community. Get the news and information you need from the award-winning writers at WBJ. Don’t miss out - subscribe today.
Worcester Business Journal presents a special commemorative edition celebrating the 300th anniversary of the city of Worcester. This landmark publication covers the city and region’s rich history of growth and innovation.
In order to use this feature, we need some information from you. You can also login or register for a free account.
By clicking submit you are agreeing to our cookie usage and Privacy Policy
Already have an account? Login
Already have an account? Login
Want to create an account? Register
In order to use this feature, we need some information from you. You can also login or register for a free account.
By clicking submit you are agreeing to our cookie usage and Privacy Policy
Already have an account? Login
Already have an account? Login
Want to create an account? Register
This website uses cookies to ensure you get the best experience on our website. Our privacy policy
To ensure the best experience on our website, articles cannot be read without allowing cookies. Please allow cookies to continue reading. Our privacy policy
0 Comments