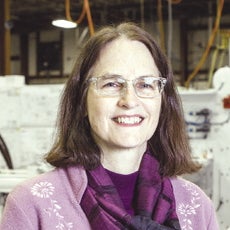
Please do not leave this page until complete. This can take a few moments.
President Donald Trump’s on-again, off-again approach to tariffs and global trade has created instability for Central Massachusetts manufacturers, who collectively rely on billions in imports of raw materials to produce their goods.
Rather than waiting for the tariff dust to settle, experienced manufacturing leaders are encouraging Central Massachusetts businesses to have a proactive response, save cash, and take an even closer look at their supply lines, as the state works to gather data to attempt to get ahead of tariff-related impacts.
Speaking during a panel discussion at WBJ’s Central Mass Manufacturing Summit & Awards on April 22, Leslie Greis, owner of Worcester-based manufacturer Kinefac Corp., said companies in the sector should carefully manage their financial resources until at least the end of the summer as the situation with tariffs continues to play out.
“I’ll cut to the chase: Conserve cash, because it’s going to be a rocky road for the next three months,” Greis said. “There’s just so much uncertainty, and I doubt it will be resolved until August or September. Not only do tariffs have to run their 90-day reprieve course, but there’s also a debt ceiling coming along.”
The constantly changing tariff landscape is forcing manufacturers to hold off on expansion efforts or big equipment purchases, said Rory Fazendeiro, a business attorney at Worcester law firm Bowditch & Dewey.
“With the tariff and import restrictions changing as quickly as they are, businesses are being forced to hold-off on significant investment in manufacturing and supply until the landscape settles,” Fazendeiro said. “Many U.S. manufacturers and producers simply have no ability to absorb tariff costs where margins are already thin. This inability to absorb tariff costs forces producers to increase their prices, which creates problems with their commercial customers and consumers.”
Massachusetts imported $5.65 billion worth of non-manufactured commodities in 2024, according to data from the U.S. Census Bureau. While that figure includes some commodities like agricultural products, it largely refers to the raw materials manufacturers will use to create their products.
The $5.65 billion doesn’t include other imported goods essential to manufacturing operations, like specialized equipment or pre-fabricated components. Machinery and instruments were in fact well represented in the top 10 list of imported goods in Massachusetts in 2021, the most recent year of data available from the Bureau of Labor Statistics’ Business Response Survey.
Precision instruments were the most imported goods, coming in at $11.8 billion, with electric machinery in second with $10.7 billion, followed by industrial machinery, at $8.2 billion. While not all of this equipment is used by manufacturers, the industry’s reliance on international trade to produce goods is clear.
“Overwhelmingly, manufacturers in Massachusetts do rely on imported raw goods and machinery to produce their products,” Ben Linville-Engler, deputy director and chief investment strategist of state agency MassTech, wrote in an email to WBJ. “This could be steel and aluminum or other rarer materials. Many raw goods are very difficult to source domestically, while others are prohibitively expensive. As a result, our local manufacturers are actively assessing whether they can shift to new suppliers for these raw goods.”
The Gov. Maura Healey Administration has launched a survey for business owners to gauge current or anticipated impacts caused by new tariffs, the first steps in an effort dubbed the Tariff Response and Business Operations Support Initiative, a state initiative to understand the impacts of tariffs.
While it’s too early to draw conclusions from the survey results, tariffs are having a notable impact on manufacturers’ plans, said Linville-Engler.
“It’s clear through our conversations with manufacturers across the state that tariffs are creating significant uncertainty, and many businesses are having to adapt their operations and growth plans,” he wrote.
Noting that a large amount of imports into the country are components and materials used by manufacturing firms, Greis said the confusion around tariffs is causing slowdowns in customers.
“This confusion just creates uncertainty problems.” Greis said. “In fact, I was on a call with Mike Davin, from the National Association of Manufacturers. He said that 56% of imports are inputs to manufacturing. So you're not doing trading, you're not going to be manufacturing, and [NAM] is pushing really hard to figure out how to nudge the [Trump] Administration along and give them ideas, because it is kind of a horrible situation we're in with this just unnavigable tariff confusion.”
Greis’ uncertainty is mirrored by others in the manufacturing space. Since December, business confidence for local manufacturers has been shaken, with the blame being pointed toward tariffs and rising costs, according to the Associated Industries of Massachusetts.
The AIM Manufacturing Index, which lagged behind overall business confidence for much of 2024, sat at 52.3 in December. By March, confidence among Massachusetts manufacturers had fallen into negative territory, at 45.1. The index is measured on a 100-point scale, where any score below 50 represents a pessimistic outlook.
The bulk of the president’s economic focus has been put toward implementing tariffs. These efforts are meant to encourage the return of American manufacturing and right what Trump sees as an imbalance between what the country’s businesses and consumers sell into the global trade market versus what they buy.
While White House trade adviser Peter Navarro has claimed the administration is aiming for a goal of 90 international trade deals in 90 days, as of April 29, the Trump Administration has yet to secure a single one.
In the meantime, implementation of some tariffs have been delayed, while others have been made even more harsh, as key trade partners like China have responded with tariffs of their own.
While manufacturers are already more likely aware of the nuances of their supply chains thanks to their dealings with the impact of the COVID-19 pandemic, Olivia Antonelli, supply chain manager for the Massachusetts Manufacturing Extension Partnership, said firms should gain a deeper understanding of every level in order to forecast possible disruptions caused by tariffs and other geopolitical issues.
“We hope our companies are having visibility down your supply chain, but we still often find that it's just at one level,” Antonelli said at the WBJ Manufacturing Summit. “But are you asking those questions of ‘Who are your suppliers’ suppliers?’ That way you can keep an eye out on the news for whatever's going on, just to get a better idea of how your company is going to be impacted.”
Manufacturers now need to spend more time focusing on their supply chains, said Fazendeiro.
“Leveraging strong relationships with supply chain partners allows for discussion and negotiation over how to share the impact of increased costs due to tariffs,” Fazendeiro said. “Other actions to mitigate tariff impacts include diversifying supply chains, assessing the feasibility of local sourcing, and negotiating payment and other terms with suppliers.”
Even with extensive knowledge of their supply chains, Fazendeiro warned the rapidly-changing situation with tariffs is largely unpredictable.
“The uncertainties over the outcome of the tariff war and government restrictions makes it very difficult for businesses to plan ahead,” he said. “The supply chain impacts faced by U.S. businesses are extensive and difficult to navigate. The tariff war is making business planning and product fulfillment nearly impossible, with the rules of the game changing every day.”
While not every manufacturer is sounding the alarm, the impact is being felt.
“The uncertainty regarding Trump's tariffs and the damage by [Elon] Musk's job and funding cuts is having a direct impact on our ability to purchase raw materials and deliver cost-effective finished goods to our customers,” wrote one manufacturer who participated in AIM’s anonymous March survey.
AIM feels an open market approach would be much healthier for manufacturers than trade wars.
“The most effective way to build the manufacturing base of Massachusetts is to provide domestic manufacturers fair access to overseas markets anxious to buy the technologically sophisticated products in which we specialize,” Brooke Thomson, president and CEO of AIM, wrote in an April post on the organization’s website, which argued Trump’s tariffs could impede the state’s economy. “Open markets represent the surest path to job growth for the commonwealth and the rest of the nation.”
Some are hoping for carve-outs for particular imported materials needed by manufacturers, but that’s easier said than done, Gries said.
“Can they figure out a way to have tariffs be less onerous for critical input?” she asked. “The problem is my critical inputs are a little bit different than your critical inputs. There's going to be some challenges for lots of people going forward.”
Eric Casey is the managing editor at Worcester Business Journal, who primarily covers the manufacturing and real estate industries.
0 Comments